Baxi Boiler Troubleshooting
Baxi is a great boiler brand and it is trusted by many up and down the country. However, there may be times when your Baxi boiler isn’t acting up to scratch. In this guide, we’ll discuss common Baxi boiler issues, how to fix them and some common error codes.
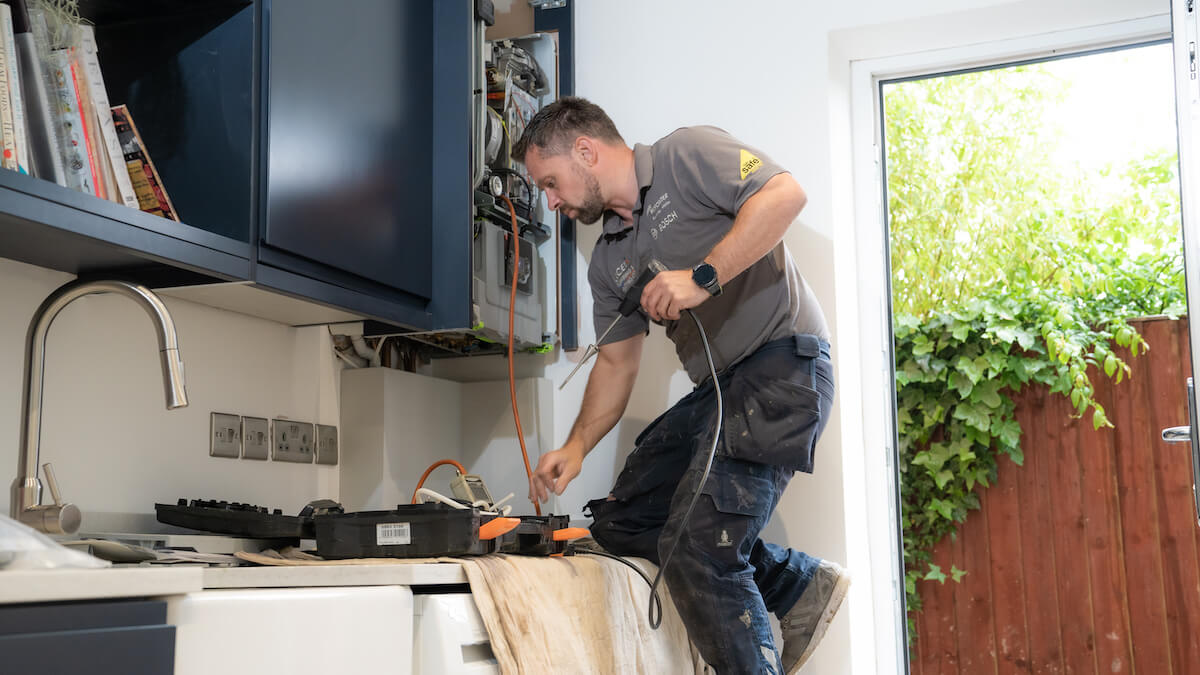
Do Baxi boilers have a warranty?
Yes, every new Baxi boiler comes with a warranty of 1 year as standard. However, depending on the model of your Baxi boiler, Baxi offers extended warranties ranging from 2 – 10 years.
You can extend your Baxi boiler warranty by following the steps below:
- 1Either you or your Baxi boiler installer should register your warranty with Baxi within 30 days of the boiler being installed.
- 2Make sure your boiler is installed by a Gas Safe registered engineer who will complete a benchmark commissioning checklist.
- 3Have your boiler serviced once a year by a Gas Safe Engineer in line with Baxi’s instructions.
If you fail to meet the requirements as stated above, Baxi will revert your warranty to 12 months from the date of installation.
Common Baxi boiler problems
Like all boilers, Baxi boilers can face a common boiler problem at some point in their lifetime.
Low boiler pressure
When looking at the pressure gauge on your Baxi boiler, the needle should be around 1.5. If the pressure drops below this, then the unit will need to repressurise.
Most boilers, if not all, will gradually lose pressure over time; but if there is a sudden drop, this could be a sign of a leak. If you suspect there is a leak, turn off your water supply and contact our team for the assistance of a Gas Safe engineer.
Get Help from a Gas Safe Heating Engineer
Frozen condensate pipe
Seeing the error codes E133 or E28 means that your condensate pipe may be frozen. The condensate pipe transports pacific water away from the boiler. This usually runs outside into a drain, but because of its location, it does face the risk of freezing.
Water leaking
There are a number of different causes for a leak, but its location will help you to determine the fault. The cause more often than not is a broken internal component, like a pump seal or pressure valve. If the leak is coming from the pressure valve, then your boiler’s pressure may be too high. If it comes from the pump seal, it may have become worn out and need replacing.
If there is a leak, you should see the error codes H.02-.06.
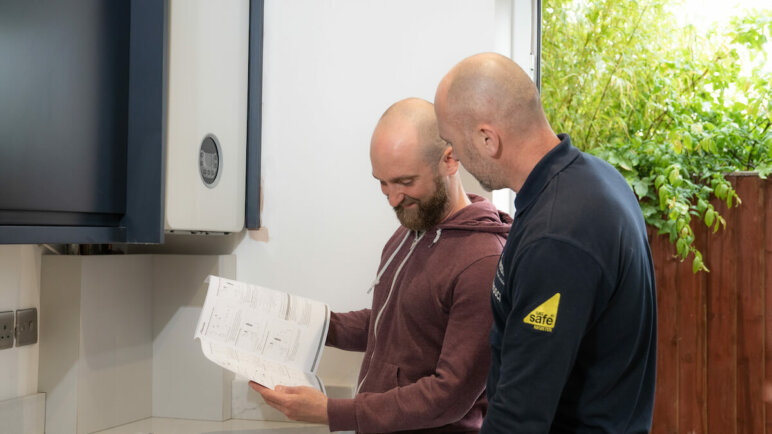
Baxi boiler not firing up
There are some simple reasons for your Baxi boiler not firing up, and these are things that you can check yourself.
Firstly, check the simple things such as if there is power to the boiler and if your thermostats and timers are on.
Secondly, check if the dials on the boiler have been changed or switched down low or off.
If you’re not seeing any error codes, then there could be an issue with the gas supply, ignition leads or a faulty gas valve. If you suspect this is the case, then it’s time to contact our Gas Safe engineers who will be able to repair the faulty parts.
How do you reset a Baxi boiler?
In some circumstances, your boiler may lock out. This is identified on a Baxi boiler by a red lockout light.
Most Baxi boilers have a simple reset button on the front panel. Once you’ve located this, press and hold the button for 3-5 seconds until the red light goes away or until it’s clear that the boiler has rebooted itself.
Baxi boiler firing but there is no hot water
There are a number of different reasons why your Baxi boiler is firing up but there is no hot water.
Pilot light not lit
*Please note that in modern boilers there is not usually a pilot light. If you have a pilot light on your boiler, it is an old model of boiler.
One of the main reasons could be because the pilot light isn’t lit. Sometimes the light fails to catch, resulting in a total failure of hot water.
If this is the case, all you need to do is check your boiler’s manual to find out how to relight the pilot. This can vary for different models, but generally speaking, all you need to do is look through the pilot window and press the gas control knob fully inward and hold. You should repeat this until the pilot ignites.
Faulty diverter valve
A faulty diverter valve is potentially caused by natural system corrosion or metallic build-up over time, meaning the hot water is only being delivered to your radiators and not your taps.
Besides from seeing a potential error code, there isn’t much you can do about this yourself. You should contact a heating engineer if you think this is the case. This way, you can be diagnosed properly and your diverter valve can be replaced if necessary.
Frozen pipes
As we’ve mentioned, Baxi boilers can suffer from frozen pipes. If the condensate pipe does freeze over, your boiler may shut down for safety reasons, resulting in no hot water at all.
Thankfully, this is a quick fix at home and you can slowly melt away the frozen area by wrapping the pipe in cloth or by pouring the warm water over the top. You can use your kettle for this, but be sure to let the water cool down slightly.
How do you fix the pressure on a Baxi boiler?
If your Baxi boiler is experiencing low water pressure (E118) don’t worry, this is something you can fix yourself using the following steps:
- 1Turn off your boiler
- 2Locate your boiler’s Easy Fill permanent filling link. This will be beneath the boiler.
- 3Pull the green lever down until the pressure gauge shows 1 to 1.5 bars of pressure, and then release the lever. Do not increase the pressure to above 1.5 bars as this can damage the boiler itself and the system.
- 4Use a cloth to catch any drops of water from the air break on the filling link. Don’t worry, a small amount of water is normal to appear.
- 5Check your central heating system and your radiators for any signs of water leaks.
If this doesn’t work, you can head over to our full guide on boiler pressure for other useful tips on how to repressurise your boiler.
Baxi boiler keeps locking
One of the main reasons your Baxi boiler keeps locking is due to overheating. The boiler will lock itself to preserve any internal components and further damage.
Other reasons why your boiler may be causing lockouts include:
If any of the above occur, you will likely see an error code on the display screen. If you have tried to reset the boiler multiple times but you’re still experiencing lockouts you should call a heating engineer to come and inspect for bigger problems.
Baxi boiler making loud noises
All boilers, including Baxi boilers, make a lot of noise. However, it’s not so easy to tell when a noise isn’t quite right. Most loud noises are described as gurgling, vibrating or banging. If you are hearing any of these noises coming from your Baxi boiler, you will likely need a visit from an engineer.
A build-up of limescale, can also create a whistling noise known as “kettling”. This can be cleaned away by engineers who will flush the system out and remove the limescale.
Other noises can be caused by air in the system, which could be fixed by bleeding your radiators.
How do you find the error codes on a Baxi boiler?
If your Baxi boiler develops a problem, the boiler will show an error code on the display screen to help you identify the issue.
Each boiler has their own set of codes, so make sure you have your manufacturers guide handy, or you know the model number so you can do a quick Google search.
Book Us to Fix your Baxi Boiler
Error Code | System Error |
---|---|
H.01-.00 | Temporary fault. Temporary loss of communication between gas valve and boiler board. |
H.01-.05 | Temporary fault. Maximum difference between the flow and return temperature exceeded. |
H.01-.08 | Temporary fault. Flow temperature increasing too fast in heating mode. Non-existent or insufficient circulation. |
H.01-.14 | Temporary fault. Maximum flow temperature valve exceeded. Non-existent or insufficient circulation. |
H.01-.18 | Temporary fault. No circulation of water. Non-existent or insufficient circulation. |
H.01-.21 | Temporary fault. Flow temperature increasing too fast in DHW mode. Non-existent or insufficient circulation. |
H.02 – .03 | Temporary fault. Incorrect configuration settings C1/C2. |
H.02 – .04 | Temporary fault. Parameter error. Incorrect parameters. |
H.02 – .06 | Temporary fault. System water pressure. Water leak on boiler. Water leak on system. |
H.03 -.00 | Temporary fault. Communication error with NTC flue sensor. Sensor not, or badly connected. Bad connection. Sensor fault. |
H.03 -.01 | Temporary fault. Communication error with the HMI PCB. HMI not connected. |
H.03 -.02 | Temporary fault. No flame during operation. No ionisation current. |
Error Code | System Error |
---|---|
E.00 – .04 | Permanent fault. Return temperature sensor open-circuit. Sensor not or badly connected. Bad connection. Sensor fault. |
E.00 – .05 | Permanent fault. Return temperature sensor open-circuit. Sensor not or badly connected. Bad connection. Sensor fault. |
E.01 – .02 | Permanent fault. Temperature measured by return sensor greater than flow sensor. Bad connection. Sensor fault. Sensor not or badly connected. |
E.01 – .04 | Permanent fault. Loss of flame detected 5 times in 24 hours (With burner on). No ionisation current. |
E.01 – .11 | Permanent fault requiring reset. Incorrect fan speed. External draught over the boiler. Defective gas/air unit. |
E.01 – .12 | Permanent fault requiring reset. Temperature measured by return sensor greater than flow temperature. |
E.01 – .12 | Permanent fault requiring reset. No circulation. Sensor not or badly connected. Sensor fault. |
E.01 – .17 | Permanent fault. Maximum flue gas temperature value reached (>140 Deg C). No circulation. Sensor fault. |
E.01 – .20 | Permanent fault. Boiler reset in progress. Reset button has been pressed. |
E.02 – .00 | No or low system water pressure. Low system pressure (less than 0.5bar) boiler will not function. |
E.02 – .07 | Permanent fault. On board CSU time-out. Check PCB for damage. |
E.02 – .16 | Permanent fault. Permanent loss of communication between gas valve and boiler PCB. Fault in air/gas unit. Loose connection to gas valve. |
E.02 – .17 | Permanent fault. Jumper 1 changed. Check position of jumper 1. |
E.02 – .19 | Permanent fault. Jumper 2 changed. Check position of jumper 2. |
E.02 – .20 | Permanent fault. Jumper 3 changed. Check position of jumper 3. |
E.02 – .21` | Permanent fault. Connection to external device unsuccessful. Check wiring to external devices. |
E.02 – .47 | Permanent fault. Configuration to external devices unsuccessful. Check pairing to external. |
E.02 – .48 | Permanent fault. Gas valve fault. Gas valve not detected. |
E.04 – .00 | Permanent fault. Flow temperature sensor short-circuited. Sensor not or badly connected. Bad connection. Sensor fault. |
E.04 – .01 | Permanent fault. Flow temperature sensor open-circuited. Sensor not or badly connected. Bad connection. Sensor fault. |
E.04 – .02 | Permanent fault. Critical flow temperature reached. Non-existent or insufficient circulation. |
E.04 – .03 | .04Permanent fault. Flue temperature sensor short-circuited. Sensor not or badly connected. Bad connection. Sensor fault. |
E.04 – .04 | Permanent fault. Flue temperature sensor open-circuited. Sensor not or badly connected. Bad connection. Sensor fault. |
E.04 – .05 | Permanent fault. Critical flue gas temperature value reached. No circulation. Sensor fault. |
E.04 – .06 | Permanent fault. Maximum safe temperature value reached. (Safety thermostat open-circuited). No circulation. Sensor not or badly connected. Bad connection. Sensor fault. |
E.04 – .08 | Failure to light (could be a gas supply issue). |
E.04 – .10 | Permanent fault. False flame signal. Short-term fluctuation of the mains. Ionisation current present even though there is no flame. The burner remains very hot (CO2 too high). Defective gas/air unit. |
E.04 – .12 | Permanent fault. Fan rotor blocked. Fan seized. Wiring to fan damaged. |
E.04 – .17 | Permanent fault. Problem with gas valve. Defective gas/air unit. |
Error Code | System Error |
---|---|
E20 | Central heating NTC fault |
E28 | Flue NTC fault, air pressure switch fault, blocked flue, blocked condensate or wiring fault. |
E50 | Hot water NTC fault |
E110 | E110 safety thermostat operated |
E119 | Water pressure switch not operated |
E125 | Circulation fault (primary circuit) |
E128 | Frequent flame failure (12 times). |
E130 | Flue NTC operated |
E133 | Interruption of gas supply or flame failure |
E160 | Fan or fan wiring Fault |
E193 | Pre-circulation fault |
E270 | Circulation fault (dry fire). |
E317 | Wrong power supply electrical frequency (Hz). |
E384 | False flame. |
E430 | Water pressure temporary test. |
Common Baxi boiler fault lights
As well as error codes, your Baxi boiler may display fault lights.
Error Light | System Error |
---|---|
1 flashes green | Maximum flow temperature exceeded. Flow temperature rise rate is too high. Excessive difference between, flow and return temperature |
2 flashes green | BL terminals on User Interaction. Controller are open circuit |
3 flashes green | No flame detected during operation |
4 flashes green | Bad connection or wiring fault. Internal communication fault |
5 flashes green | Parameter error or faulty PU. Configuration error or PCB fault |
6 flashes green | Possible fault Internal fault in combustion control unit |
1 flashes red | Bad connection to flow or return temperature sensor |
2 flashes red | Over-temperature thermostat on heat exchanger activated. No water flow through the heat exchanger. PCB over-temperature condition. Flue fault resulting in. Recirculation or activation of air pressure switch (if fitted) |
3 flashes red | No ignition. No flame detected following ignition. False flame signal detected |
4 flashes red | Fan calibration error. Fan failure |
5 flashes red | Bad connection to PU. Parameter error or faulty PU |
6 flashes red | Possible fault. Bad connection or wiring fault. Parameter error |
More like this
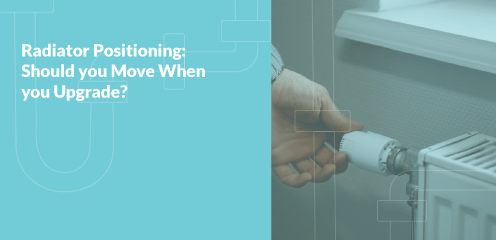
Radiator Positioning: Should you Move When you Upgrade?
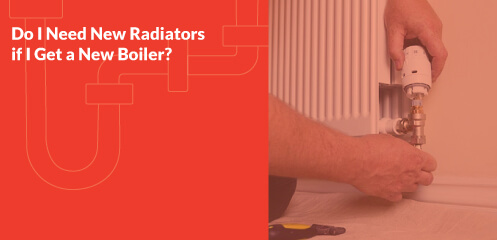
Do I Need New Radiators if I Get a New Boiler?
Find Us On
Unit 11 Eton Business Park
Eton Hill Road, Radcliffe, M26 2ZS
Opening Times
Mon – Fri 8am – 5pm
Call Us Today
0161 884 1109
GET IN TOUCH
